Casting polyurethane wheel process flow
-
01
Design mold
- Design drawings and silicone molds according to customer requirements. Pay attention to details when demolding.

-
02
Clean wheel core
- Use a detergent to remove oil stains, residual rubber and other debris on the surface of the wheel core.
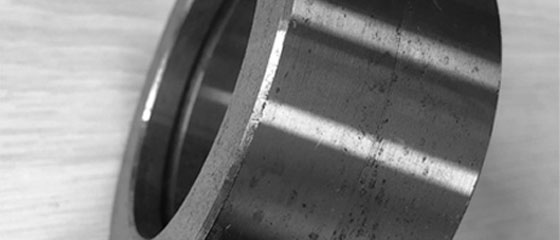
-
03
Grinding and sandblasting
- Grind and sandblast the surface of the roller core to increase the bonding between the wheel core surface and the polyurethane coating.
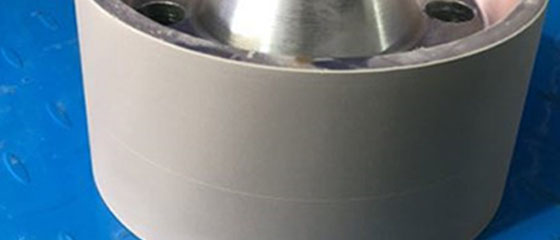
-
04
Raw material preparation
- According to the performance requirements of the wheel, prepare polyurethane raw materials such as high load, high and low temperature resistance, anti-static, and traceless.
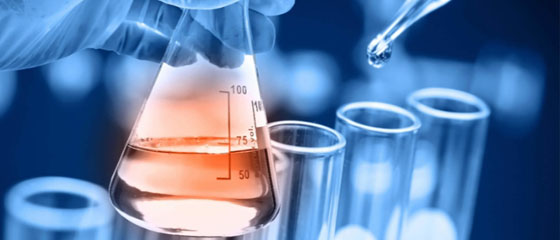
-
05
Casting polyurethane
- Rotate and cast on the surface of the wheel core that has been pre-coated with adhesive to make the wheel core and the polyurethane colloid more firmly and fully bonded to avoid bubbles.
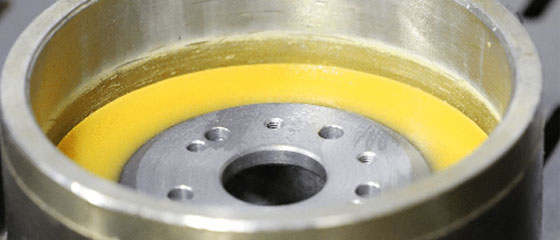
-
06
Vulcanization of polyurethane wheels
- After vulcanization, the wheel core is tightly combined with the colloid, and the PU rubber-coated wheel can be demolded after curing.
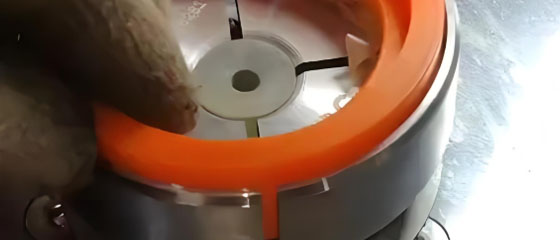
-
07
Finishing treatment
- Turn and remove burrs according to the size and shape required by the drawing, and use a CNC grinder for mirror polishing as needed.
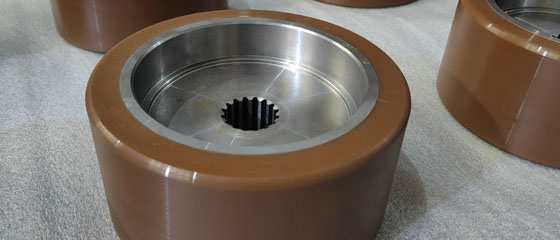
-
08
Packing and delivery
- After the quality inspection is completed, the corresponding quality inspection report, raw material certificate and delivery details will be issued, and then carefully packed and shipped.
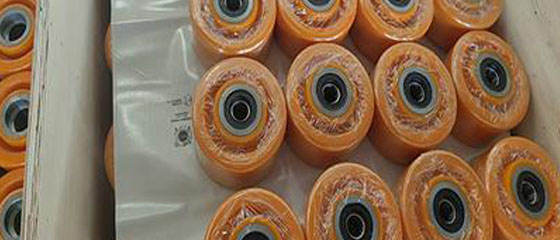
Philson has professional testing equipment, processing equipment and engineers with decades of experience in polyurethane mixing. We can customize the production of polyurethane rubber wheels with different performance requirements, such as high temperature resistance, low temperature resistance, anti-static, anti-slip or non-marking, high load-bearing, quiet, impact resistance, corrosion resistance, etc.